Application Principle of Bonding Technology for Powder Coating
Bonding technology of powder coating is also called hot bonding technology. It is mainly to make the surface of powder particles have certain viscosity by friction heating or jacket heating, so as to combine metal effect pigment and powder bottom powder.
Specifically, through the high-speed rotation of the stirrer paddle of the bonder, the high-speed collision and friction between the powder and the powder, metal effect pigment, powder and the bonder (stirrer paddle, cylinder wall) are made;
In a certain period of time, when the surface temperature of powder particles rises to a certain degree, the surface of powder softens, and the metal effect pigment particles are bonded with the powder coating particles, so that a stable metal effect coating can be obtained during electrostatic spraying.
In order to make the coating effect more stable, under a certain content of metal effect pigment, bonding technology is adopted to make more metal effect pigment and powder tightly combined to ensure the construction stability.
Powder coating is a material which is composed of resin, curing agent, pigment, auxiliary agent and filler. The resin in the formula is polymerized by polyol and polyacid.
Glass transition temperature refers to the transition temperature of amorphous polymer (including the non crystalline part of crystalline polymer) from glass state to high elastic state or from the latter to the former. It is the lowest temperature for the free movement of macromolecular segments of amorphous polymer, usually expressed in Tg.
There is a certain fluctuation with the change of measurement methods and conditions. Above this temperature, the polymer shows elasticity; below this temperature, the polymer shows brittleness. As shown in the figure below, it is the shape temperature curve of polymer.
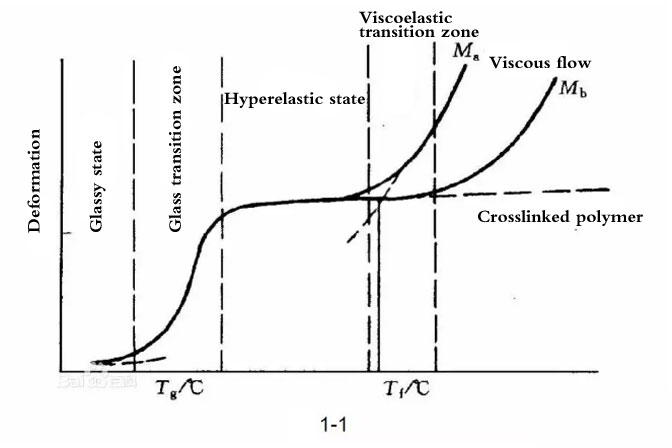
The setting conditions of bonding process mainly include bonding temperature, heating speed, holding speed and holding time. The reason why the metal effect pigment and powder particles are bonded together is that the surface of powder particles has softened or even become sticky. At this time, the instantaneous temperature on the surface of powder particles has reached the softening point.
When there is friction between the impeller and the material, part of the work done by the impeller on the material is converted into the kinetic energy of the material, and part of the work is converted into the thermal energy, so that the instantaneous surface temperature of the powder particles reaches the Tg point, or higher than the Tg point.
At this time, due to the huge force of the stirring paddle on the material, the powder particles are tightly bonded with the metal effect pigment. The electron micrograph of bonding powder product is shown in the figure below.
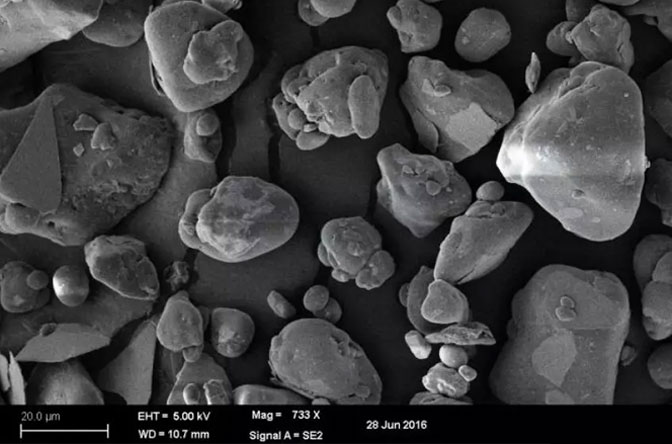
The powder coating of common products is composed of resin, curing agent, pigment, filler and auxiliary agent. Products obtained by premixing, melt extrusion, cooling, crushing, fine crushing and grading screening.
Therefore, the products with good mixing effect can be regarded as each powder coating particle with the same composition and charged performance, and the charged amount of powder particles is uniform under the action of high-voltage electrostatic. According to Coulomb's law, in a certain period of time, the electric charge of powder coating particles has the following relationship:
Q
s=3πε
0(ε-1)/(ε+2)d
2E
Among them:
Q
s: Electric charge of powder particles;
ε: Dielectric constant of powder;
d: Particle size of powder particles;
E: Applied electric field strength;
ε
0 = (819 ×10-11)F/m.
Therefore, the color, appearance and performance of the same powder coating are the same when it is sprayed and baked. When the recycled powder is used repeatedly, the color, appearance and performance of the coating are basically stable.
According to the requirements of coating appearance, when the metal effect pigment is added to the powder coating by dry mixing method, the charging effect of metal powder and metal effect pigment is quite different from that of powder when the powder has static electricity under the action of high voltage static electricity.
Therefore, the proportion of the powder adsorbed on the workpiece to the metal effect pigment is different from that of the original powder and the effect is not stable, which will lead to the inconsistency between the proportion of the metal effect pigment in the recycled powder and the metal content in the new powder.
With the increase of recovery times, the difference of metal content is more and more big, so when the recycled powder is added for spraying, the color and appearance of the coating changes with the spraying time, resulting in the instability of coating quality.
In order to ensure the stable appearance and quality of metal powder (metal effect pigment) in electrostatic spraying products, special process must be adopted to deal with the powder coating to ensure the coating quality of metal powder (metal effect pigment).
This treatment process is called "bonding", so bonding treatment must be carried out in the production of products with metal effects (aluminum powder, pearlescent powder, copper gold powder, nickel powder, zinc powder).
In the process of electrostatic spraying, in addition to the electric field force, the powder coating particles have their own gravity, air resistance and air pressure.
Therefore, combining formula (1) we can see that the factors that affect the charge quantity QS of powder include dielectric constant, particle size of powder and electric field strength.
The dielectric constant is mainly affected by the powder material and bonding stability, and the electric field strength is affected by the voltage and gun distance.
In the spraying process, to maintain the stability of the spraying effect, we should try to make the gravity, electric field force, air resistance and air pressure of each powder particle equal, and the direction is the same.
The factors of spray stability are bond stability (the combination degree of powder and metal effect pigment), voltage, current and air pressure. Therefore, the hand spray gun can judge the bonding stability by spraying different voltage and air pressure to observe whether the coating color and metal effect are consistent.
The factors that affect the stability of bonding include bonding temperature, bonding time, operation frequency, transition frequency, feeding sequence, resin content of the bottom powder, particle size of the bottom powder, types of metal effect pigments and the content of metal effect pigments.
Bonding process is a general term of bonding temperature, bonding time, heating frequency, transition frequency, cooling time and feeding sequence.
In order to make the powder coating with metal effect pigment obtain stable film quality when it is applied with electrostatic powder spraying, the metal effect pigment particles are bonded to the powder coating particles under certain temperature conditions, and the metal effect pigment is evenly and stably adsorbed to the workpiece in a certain proportion during electrostatic spraying, so as to ensure the stable appearance and quality of the film.
The setting of temperature is the main factor of bonding, which is mainly set according to the glass transition temperature of powder bottom powder. Generally, the bonding temperature of plane metal powder is several degrees higher than the glass transition temperature.
In general, if the metal powder is not bonded, the content of the metal effect pigment in the recycled powder will gradually increase with the increase of the recycling times, because the electrostatic capacity of the metal effect pigment is different from that of the base powder.
When the recycled powder is used for spraying or when the recycled powder is added for spraying unevenly, the appearance of the original powder spraying will be different, and the appearance and quality of the coating film will be unstable.